Tools
Empowering your decision making with interactive scenario planning capabilities and graphical insights.
Empower your decision making with interactive scenario planning capabilities and graphical insights.
Since its inception, Sequoia’s Tools offering has evolved from complex, somewhat impenetrable spreadsheets to robust Excel-based tools and, most recently, graphically interactive web-enabled services. Each iteration has aimed to provide tools that help Supply Chain teams use data for informed, economically sound decisions and facilitate insightful discussions within the Supply Chain function and across boundaries.
By transferring knowledge; building client capability through both appropriate tools and supporting skills, teams can continue to drive results long after our specific assignment has finished.
A focus on usability of software to deliver results.
Our applications are constantly improved to deliver tools that are easier to use, incorporate the latest thinking and are specifically tailored to your business. We have built dozens and dozens of Supply Chain models and have learnt from our own experience how to present information in an easily digestible form to support successful decision making.
Our tools offer flexibility, interactive data with clickable charts, drill down options and dashboards to ensure that decisions, whether strategic or operational, are driven by a comprehensive understanding of appropriate Supply Chain data.
Can we make effective decisions in S&OP meetings?
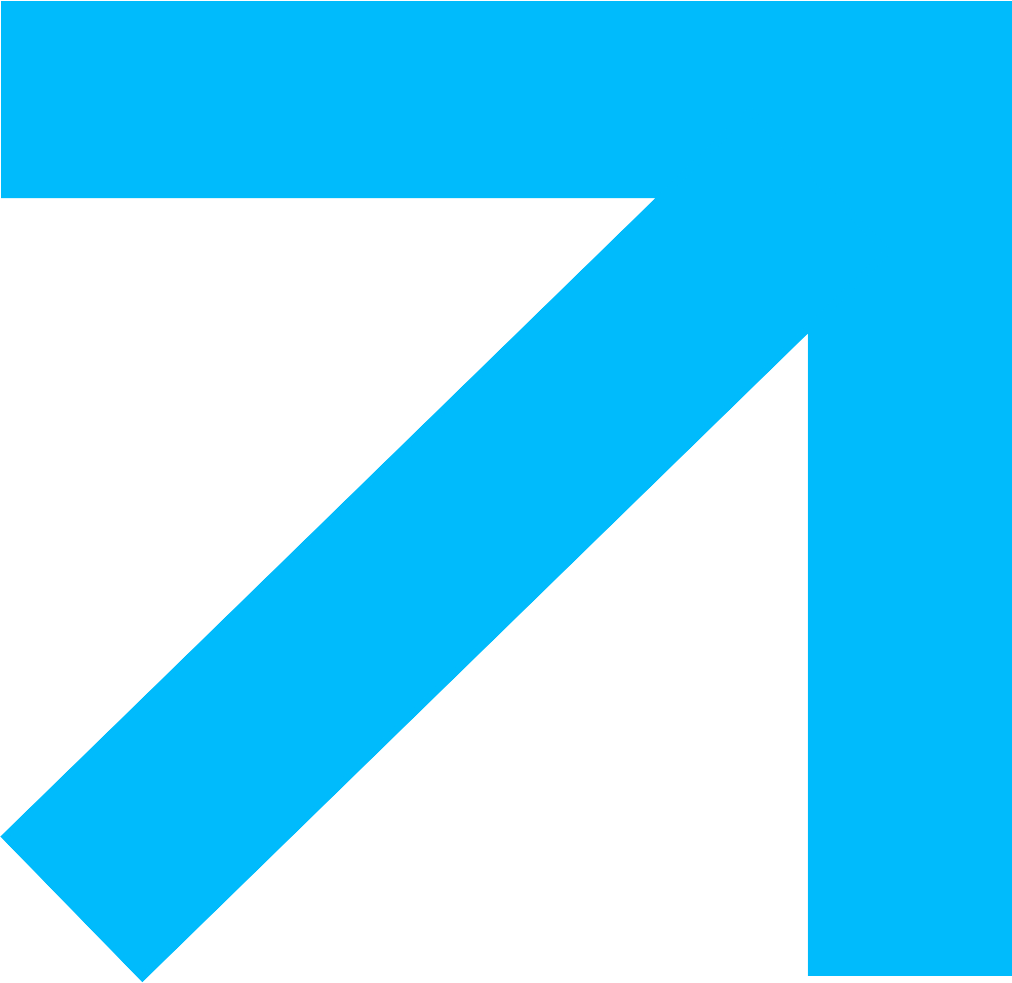
Our client was a private label supplier of complex, chilled ready meals with a 1–2 day shelf life. This meant:
- The order to dispatch cycle was measured in hours, so S&OP functions were closely tied to factories.
- Product complexity caused unpredictable capacity pinch points daily and weekly.
To improve the cross-functional S&OP process, Sequoia built a graphical capacity model using SAP ERP master recipe data:
- Capacity was modelled by process and day, visualising in-week cycles and promotional effects live during S&OP meetings.
- Drill-down features allowed analysis of which SKUs impacted specific processes at any time.
- What-if capabilities enabled real-time adjustments to forecasts, shift patterns, and processes during live discussions. Changes were non-destructive, allowing easy resets or saving as scenarios.
An Inventory Policy that takes in to account ALL the variables?
A large, complicated, Direct Sales client has experienced consistent and challenging sales growth and ever increasing geographical and SKU complexity. Forecasting is distributed to markets and procurement is via a globally distributed supply base. The net result is that inventory management priorities are extremely difficult to assess and communicate.
Sequoia were asked to build an inventory policy model, leveraging several of our skills:
- Core code components to evaluate the relationship between inventory and business parameters
- Handling large, complex data sets
- Creating interactive, graphical tools
We developed a Board/Exec level graphical tool to evaluate and communicate inventory improvements. The tool:
- Allows analysis at the company level or for selected countries, brands, and categories
- Computes aggregated inventory-driving parameters (e.g., Forecast Accuracy and Lead Time)
- Displays data graphically with customisable axes
- Supports 'What If' analysis for improvements in driver parameters
- Allows drill-down to SKU/location levels to identify issues or improvements.
The days of clunky Safety Stock Tools are over.
After years of assuming someone would create a tool to set ERP parameters precisely, Sequoia has developed our own. OnTarget is our web-enabled Inventory Management application, which encapsulates over two decade’s worth of experience in setting FMCG parameters.
Incorporating the complexities of FMCG reality; variants, seasonality, events, intermittence and obsolescence risk, it has transformed performance wherever it has been deployed. The graphical interfaces and presentation of science-based parameters facilitates rational discussion and challenges ways of working. For a more in-depth understanding, please visit our dedicated OnTarget page.
Our platform
Sequoia OnTarget®
Transform Supply Chain management through understanding, visibility and collaboration, with Sequoia’s cloud-based control and optimisation platform.